Polyurethane model and tool boards
The creation of models and tools has gone through deep transformations in a relatively short time. The transition from manual processing to processing by milling and CNC centers required the replacement of traditional materials (wood, alloys, light metals) with synthetic materials that are easy to process and have very good dimensional stability.
Polyurethane boards can be divided primarily according to their density into modeling boards and tool boards. It is possible to choose between different boards with a density from 0.08 to 1.7 kg/dm³. A wide range of densities makes it possible to select suitable boards in terms of surface quality and mechanical properties.
Light boards with a density of up to 1000 kg/m³ are easy to process. The most important advantage of these boards is their low density with relatively high hardness, so they can be used for easy control measurements and details that can be quickly processed and finished.
Medium-density boards of 1200-1500 kg/m³ are more demanding to process, but clearly have better mechanical parameters, including a hardness of 82 Shore D, and often higher impact and abrasion resistance than boards with a lower density. They are used as plates for molds for thermoforming, as plates for foundry models, for molds and models for laminates and for the production of finished details in advertising and industry.
The most valuable on the market are boards with a density of 1600-1700 kg/m³. They are more difficult to process and have a higher price than boards with a lower density, but they are characterized by high dimensional stability against temperature changes and high hardness. When high-density tool plates have good heat resistance combined with their good dimensional stability, they can compete with aluminum, for example, as a raw material for thermoforming molds, sheet dies, foundry models and gauges.
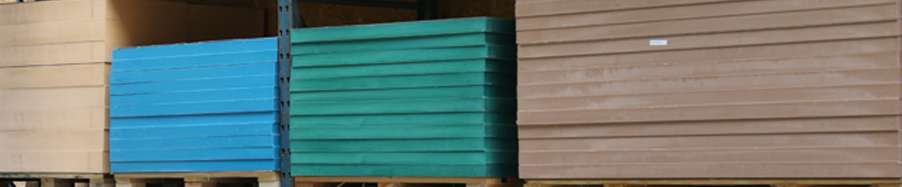